Products
Solutions
Resources
9977 N 90th Street, Suite 250 Scottsdale, AZ 85258 | 1-800-637-7496
© 2024 InEight, Inc. All Rights Reserved | Privacy Statement | Terms of Service | Cookie Policy | Do not sell/share my information
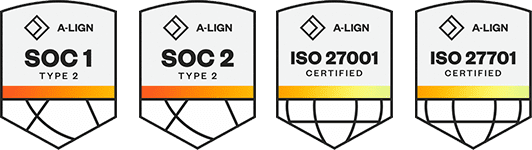
One of the standard forms of contract payment terms in the construction industry is based on the value of specific contract deliverables. It is also based on the work completed during the previous month towards those pay items. Throughout the life of a project, you will want to track the progress of work completed.
It is important to identify and define a few key terms related to progress measuring, and to identify how to utilize InEight Control as a tool for accessing and maintaining critical job factors.
Within InEight Control, you can maintain an Original Budget, a Current Budget, and a Current Estimate, as is shown from the CBS tab of the Control main page by using a custom data block.
The Original Budget (OB) is a snapshot of the project plan in its original state, prior to execution. It is a baseline used for comparison as the project progresses. You cannot edit your Original Budget values; they are read-only in the CBS register, available for reference only.
Once set, the Original Budget never changes.
Within the CBS register of InEight Control, you will find the Original Budget (OB) values for man-hours, quantities, and costs.
The Current Budget (CB) is the project’s operational budget, including only project changes approved through a controlled process. The Current Budget is therefore the sum of your Original Budget, plus or minus any approved changes.
See the Change Management lesson for more details on managing and approving budget changes.
Within the CBS register of InEight Control, you will find Current Budget (CB) values for planned, earned and forecasted costs, hours and productivity.
The Forecast (T/O) - CB qty delta column shows you the difference between the Forecast (T/O) quantity and the current budget total quantity columns.
The calculation for this formula is [Forecast (T/O) qty] - [CB total qty].
You can filter on non-zero CBS records, which makes you aware to update either the Forecast T/O Quantity or CB Total Quantity.
The Current Estimate (CE) represents the most up to date estimate of your work. You can update your Current Estimate quantities, hours, and costs at any time in the CBS register, with no required approval process or work flow.
You can use the Current Estimate as a “sand box” to build out change orders and do what-if analysis to plan for potential changes, without worrying about affecting the Current or Original Budgets.
Within the CBS register of InEight Control, you will find a wealth of columns for measuring and analyzing your project progress. InEight Control uses its own terminology for these measurements that match up well with common Earned Value Management terminology. Before comparing these terms, the following section reviews some Earned Value Management basics.
The different ways to update the Forecast (T/O) quantity include:
Direct entry into data block.
Direct entry into Cost item details slideout.
Excel import.
Undo.
Copy/paste into data block.
Rolldown from assigned pay item (need to have this setting enabled).
Cost item API.
Selective import.
Rolldown from parent (Qty driver is Superior CI).
Rollup from children ( Contribute qty is checked).
When you update the Forecast (T/O) on both the CE and the Forecast, you are prompted to update either the CE unit cost for CE total cost. You can also choose to update either the CE labor cost/Mhr or CE total MHrs, and either CE construction equipment cost/hr or CE total equipment hrs (if applicable).
This will then update the Forecast values because Forecast is based off Remaining qty * selected unit cost, and your Remaining qty will update with a Forecast (T/O) qty change. This also affects your % complete (Qty claimed / Forecast (T/O) qty) which impacts all the earned value columns. It will also update the Forecasted revenue values as well (based on the % complete).
You can easily filter the Forecast (T/O) - Plan component qty delta column. There is also a menu option in the Actions menu to update the Forecast (T/O) qty to match the Plan qty - Update Forecast (T/O) qty with Plan component total qty
Planned Value (PV) are the costs and hours you have estimated and scheduled for the project. Think of PV as your approved budget of scheduled items. In Control, your PV includes the following columns:
CE Total Cost
CE Total MHrs
CB Total Cost
CB Total MHrs
Earned Value (EV) Measures the amount of money you merit in return for the work performed up to that point. You can use EV to measure how much of your planned costs and hours you should have spent so far, according to the percent of work completed. It uses the below formula to calculate this:
Planned Value x % of work completed = Earned Value
In InEight Control, your EV includes the following columns:
CE cost earned
CE MHrs earned
CB cost earned
CB MHrs earned
Schedule performance index (SPI) measures how close the work is being completed according to the designated schedule. It is Earned value/Planned value, and is calculated as earned current budget cost/CB planned value (to date)
The SPI calculation uses the time phased budget values as planned values. To accommodate the time phased budget values, the planned value includes the cumulative time phased budget planned value to date.
Actual Cost (AC) refers to the costs you incur when you perform the work.
In InEight Control, AC is known as Total Cost (To Date). In addition, InEight Control refers to actual man-hours as MH (To Date).
Variance is the difference between EV and AC, expressed in the following equation:
Earned Value - Actual Cost = Variance
It indicates if you are performing better or worse than planned up to that point. InEight Control uses the term Gain/Loss (G/L) rather than variance, including the following columns:
CE actual cost G/L (to date)
CE MHrs G/L (to date)
CB actual cost G/L (to date)
CB MHrs G/L (to date)
Remaining is a general finance term for money that is not yet used. InEight Control uses the following terms:
CE remaining cost
CB remaining cost
These terms refer to a very specific relationship expressed in the equation:
Planned Value - Actual Cost = Remaining Value
In other words, it is the difference between what you originally planned and what you have spent so far, to help you understand how much cost or how many man-hours you have left.
The table below summarizes each EVM term with its equivalent term in InEight Control and what it measures.
EVM Term |
InEight Control Term |
What it measures |
---|---|---|
Planned Value (PV) |
CE total cost CE total MHrs CB total cost CB total MHrs |
Budget of scheduled values |
Earned Value (EV) |
CE cost earned CE MHrs earned CB cost earned CB MHrs earned |
Planned Value x Percent Complete |
Actual Cost (AC) |
Actual cost (to date) Actual MHrs (to date) |
Actual/expended values |
Variance |
CE actual cost G/L (to date) CE MHrs G/L (to date) CB actual cost G/L (to date) CB MHrs G/L (to date) |
Difference between Earned Value and Actual Cost |
Remaining |
CE remaining cost CB remaining cost |
Difference between Planned Value and Actual Cost |
The following displays Planned vs. Earned vs. Actual values within a custom data block of the CBS register of InEight Control:
If you are the contractor building a project, you will need to monitor the performance of your crews, including how productive they are and how much they are being paid.
Productivity is a measure of effectiveness. The rate of output per unit of input. An example would be if you have estimated that you can install a light switch in 1 hour and it takes you 1.5 hours you are not being very productive. In InEight CB-PF is productivity and can be measured with the following equation:
Compensation is the amount of money paid to an employee for their hours worked. Compensation Factor is a numerical value comparing the budgeted compensation to the actual compensation. An example would be if you had budgeted using master electricians (making $35/hour) to install light switches, but you actually used 2nd year apprentices (making $26/hour) where you would have a compensation factor that is off. In InEight, Compensation Factor is displayed as CF (To Date). You can calculate it as follows:
Labor Efficiency Index (LEI) is a numerical value assigned to indicate the effectiveness of resource utilization. You can calculate LEI using the following formula:
Labor Efficiency Index = Productivity x Compensation Factor
.90 = .67 x 1.35
If LEI is greater than 1, it means that you are using your resource effectively.
If LEI is lower than 1, it means your resources are being used poorly.
The Plan component total qty column shows the sum of the component quantities from Plan and Control and lets you update the Forecast (T/O) qty to match this value.
Using the Install conduit cost item as an example, it is assigned to WBS phase code 1139 in the CBS.
In Plan, WBS phase code 1139 is assigned to components Conduit material with a quantity of 150 and Install conduit with a quantity of 120.
In the CBS, the Plan component total qty for the Install conduit is 270, which is a total of the two WBS 1139 components in Plan.
The Forecast (T/O) - Plan component qty column is the difference between the Forecast (T/O) and the Plan component quantity.
The Update Forecast (T/O) qty with Plan component total quantity option located under the Actions drop-down, copies the Plan component total quantity over to the Forecast (T/O) quantity. You can also right-click in the context menu to see this option.
Additional Information
9977 N 90th Street, Suite 250 Scottsdale, AZ 85258 | 1-800-637-7496
© 2024 InEight, Inc. All Rights Reserved | Privacy Statement | Terms of Service | Cookie Policy | Do not sell/share my information